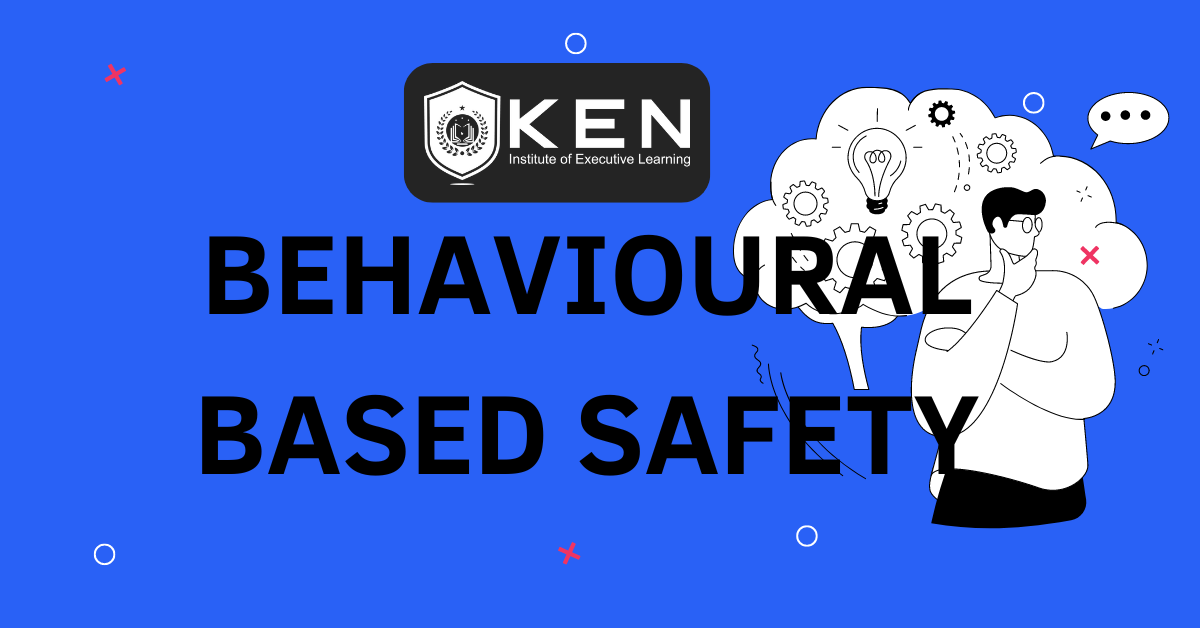
BEHAVIORAL-BASED SAFETY
Behavior is what a person does or says, as opposed to what he or she thinks, feels, or believes. Behavior-based safety refers to the use of applied behavior analysis models to achieve continuous improvement in safety performance. In-depth research about what works and what doesn’t.
Behavior-based safety programs appeal to companies because they make health and safety seem simple, do not require management change, focus on workers, and seem cheaper than correcting hazards.
The ABCs of BBS
A – Antecedents
Antecedents are pre-existing sensory or intellectual inputs that trigger behaviors and influence decision-making.
Antecedents tell us:
- What to do to receive a consequence
- What can be tangible/concrete or intangible/abstract
- What can be only as powerful as the consequences that support them
B – Behavior
Behavior refers to acts or actions by individuals that can be observed by others. To implement proper planning for safety behavior must be observable, and measurable at “Anytime, Anywhere, Anybody”.
C – Consequence
A consequence is simply what happens to the performer as a result of the behavior.
A consequence can be:
- Positive or negative (helps or hurts).
- Immediate or future (When will it occur).
- Certain or uncertain (probability of occurrence)
Elements of a Behavior-Based Safety System
1. Formal standards for behavior and performance:
- Vision, mission, values, priorities
- Policies, Plans, Processes, Procedures, Practices
- Communicated and understood by all
2. Resources to meet/exceed standards:
- Physical- tools, equipment, materials, workstations, facilities
- Psychosocial -workload, time, education, training, scheduling, culture, leadership, trust
3. A system of measurement
- Measurement – Observation and quantification
- Criteria- Performance evaluated against established criteria.
- Formal observation and feedback
4. Effective Consequences
- Soon – Certain – Significant – Sincere
- Must increase desired behaviors.
5. Appropriate application
- Selection criteria for recognition and reward.
- Presentation. Who, what, where, how and when?
- Fairness. Consistently applied laterally, vertically
6. Continual evaluation of the system
Leadership-Based Safety
Behavior-based safety relies on trust between labor and management. Management and labor must each earn that trust. Management is important, but without strong leadership, all you get is a nice set of safety manuals and a series of failed attempts at system improvement.“Concrete Leadership is the key”
Behavior-Based Safety Management
- Emphasis on consequences to influence behavior.
- Does not attempt to measure (but does not ignore) attitudes because it’s very complex.
- Motivation: Receive positive consequences
- Frequent positive reinforcement
- Frequent recognition and Occasional reward.
The key Criteria for Successful BBS Management
- There should be a system of accountability in place that defines roles and ensures knowledge to fulfill the roles at every level from worker to CEO.
- The system asks for, allows for, requires, and ensures participation at each level.
- BBS must define critical behaviors at each level of the organization – bottom to top.
- Ensure each person clearly understands the required behaviors. 5. Accurately identify and measure the presence of behaviors
- Reinforce appropriate behavior with soon, certain, significant, and sincere recognition.
Factors That Influence Safe Behaviors
Motivation Strategies:
To be effective, it must increase desired behavior. To get something and perform far beyond minimum standards the focus should be on success:
- The worker performs to receive the consequence
- Workers may perform far beyond the minimum
- The only strategy that works to increase discretionary effort
- The focus is on excellence-based success
- If one reports a hazard, he/ she is recognized.
- If one prevents an injury or saves money, he/ she is rewarded.
- Negative Reinforcement
With the intent to increase desired behavior and to avoid the negative consequences, your focus should be only on compliance for:
- The worker performs – fear-based
- A worker performs to a minimum standard – just enough to get by
- Workers can work well if the focus is on
- “If one compromised with safety rules, he/she won’t be disciplined.”
Consequences That Decrease Behavior
Punishment – Punishment does not predict what the replacement behavior will be. It is usually unintentional. To stop undesired behavior, the clear instructions must be indicated:
- You get something you don’t want when you misbehave.
- If you engage in horseplay, you will be suspended from work.
Extinction – In Behavioral Based Safety, Extinction expresses “Withdrawal of positive reinforcement. You work in a culture that ignores performance”. It doesn’t matter how hard you work:
- The worker eventually performs without expectation of consequences (other than wages)
- A person is ignored – no relationship with management
- Extinction is epidemic in organizations
- Apathy is rampant, but who cares, “It doesn’t matter how hard I work around here.
To be effective, the consequences should be:
Soon – occurs immediately after the behavior/performance or as soon as possible. The more time it takes to recognize, the more significant the recognition must be.
Sure- employees should know-
- they will be recognized and understand what’s required to get recognized.
- the BBS plan specifies precisely what must be done to get the award.
- limit the number of rewards any one person can receive during a given period
- If the same person may receive the reward most of the time, allow a pass-around reward. When this occurs, the reward is not contingent on behavior.
Significant – Significance is perceived as more than an entitlement. The BBS plan assumes that the same form of recognition is desired by all. The receiver of a reward defines the nature (positive/negative) of the reward. One employee’s reward might be another’s punishment.
Sincere – genuine appreciation or disapproval. Motives for recognizing are not questioned. The principle is
“Recognize in public, reprimand in private!”
To be effective, it should be checked before recognition is given:
Is it a matter of policy or genuine appreciation?
Is the purpose of the recognition to make management, or only for the employee look good?
Micro Approach to BBS
Improvement is achieved primarily by changing the behavior of the hourly employee.
The Safety Improvement Process:
- Identify critical problem behaviors: These become action items to work on.
- Identify root causes: The “basic things” that need to be fixed to eliminate the problem.
- Generate potential actions: Think of as many solutions as possible.
- Evaluate possible actions: Choose those that are most productive.
- Develop an action plan: To carry out the chosen solutions.
- Implement an action plan: Carry the change. Limit variables.
- Conduct follow-up: Problem solved? Measure and evaluate.
Safety Training Observation Program (STOP)
STOP for Management: a comprehensive training program that teaches managers, supervisors, and team leaders how to become more skilled observers of unsafe acts, take action to prevent their recurrence and encourage safe work practices.
STOP for Employees: Teaches employees how to observe and audit themselves to prevent injuries and improve safety performance.
STOP Audits: Teaches employee self-audits (independence) and observation and feedback to peers (interdependence).
Macro Approach
Permanent improvement is achieved through cultural change
- Assess and analyze the culture and belief systems in place.
- Educate and train to affect the attitudes of line managers, supervisors, employees
- Encourage structured involvement of all employees in problem identification and problem-solving
- Reinforce key concepts such as awareness, responsibility, self-observation, and self-management.
- Provide ongoing support and commitment
- Observe behaviors and provide feedback.
- Tailored to specific needs of the workplace.
- Apply strategy to all organizational levels
Organizational Levels
Organizational Level – Includes culture with values, commitment, and behaviors that reflect a clear vision. Focus on process measures, not only on results measures.
Self Level – Includes personal responsibilities/accountabilities. Self-attitudes and behaviors
Peer Level – Includes peer interaction and support for safe attitudes and behaviors
Leader Level – Includes consistent safety commitment/communications/messages
Common Obstacles to Behavioral Change
- Management has assumed responsibility for safety and supervisors play the role of “safety cops.” Safety in such workplaces is perceived as a negative.
- The safety message is not getting out because downsizing has reduced the number of individuals available to communicate it. Meanwhile, rising production demands are increasing pressure to cut corners.
- Less time for supervisors to spend on safety training and reinforcement.
- Supervisors are often poor role models, taking shortcuts themselves and failing to follow company and OSHA rules.
- Supervisors ask employees to take risks, either implicitly or explicitly.
- Supervisors condone or overlook risk-taking behavior until an injury occurs, and then they counter it with discipline.
- Line employees hold on to tenacious beliefs such as: “Accidents don’t happen to me.”
- There is a lack of trust and communication between labor and management.
- Fear of job loss is prevalent and negatively impacts morale and job performance.
Core Beliefs That Influence Behavior on The Personal and Organizational Level
- All injuries are preventable.
- All employees are responsible for their safety and the safety of their co-workers
- Management is ultimately responsible for the safety of all employees.
- Working safely is a condition of employment.
- All risks will be identified, addressed, and managed.
- Educating and training employees to work safely is essential.
- Preventing injuries is a good profit center activity.
- Safety, production, cost, and quality depend on each other.
- Safety will never be compromised for production or convenience. • Every employee must shut down an unsafe operation.
- The continuing health and wellness of each employee is vital to our long-term success.
Integrated Approach
Culture and individual behavior are both important components and reflect “active caring”
Safety Performance Solutions (SPS)
Total Safety Culture requires continual attention in three domains.
- Internal Personal Factors: Knowledge, skills, abilities, intelligence, motives, personality, attitude.
- External Environmental Factors: Complying, reporting, coaching, recognizing, communicating, actively caring Equipment, tools, machinery housekeeping, temperature, engineering, standards Operating procedures, rules.
- Behavior Factors
Principles that Define Behavior-Based Safety
- Focus interventions on observable behaviors. Address it independently from attitudes, and opinions.
- Look for external factors to both understand and improve behaviors. Easier to define and correct, objectively, and change directly. Independent of feelings.
- Direct behavior with activators (antecedents) and motivate behavior with consequences. Activators tell us what to do.
- Focus on positive consequences to motivate behavior. It results in behavior beyond compliance, increases the frequency of desired behaviors, and improves morale.
- Apply the scientific method to improve interventions. Rather than “common sense,” or intuition, which is usually biased.
- Use theory to integrate information but not to limit possibilities.
- Design interventions with consideration of internal feelings and attitudes. Intervene to increase feelings of control, accomplishment, and personal freedom.
Basic Strategies to Influence Behavior
- To change attitudes: in the belief that our behavior is consistent with our attitudes, you should accurately determine the proper attitude.
- To build a psychological climate (motivation): in which people will choose to behave as they wish, since that behavior helps to satisfy their current needs. You have to understand the difference between a tough controlling culture and a tough caring culture.
- To modify behavior: through the systematic use of reinforcement following behavior to influence future behavior, you need to modify the behaviors.
What Behavioral-Based Safety does not do:
- Does not turn safety over to any one level of the organization.
- Does not shift responsibility or accountability away from management to the employee. It is dangerous to promote the idea that “our employees own the safety program.
The basic truth is that safety is line management’s responsibility. Management has a legal responsibility for safety, that’s why, OSHA Law holds the employer accountable, not the employee.
“Join Ken Institute for comprehensive Safety Courses led by expert faculty, ensuring your readiness to tackle workplace fire emergencies effectively.”
Get in touch with us at: info@keninstitute.com
Visit our website: www.keneducation.in
Call us on +917569034271
Let’s connect on Facebook, YouTube, LinkedIn, and Instagram.