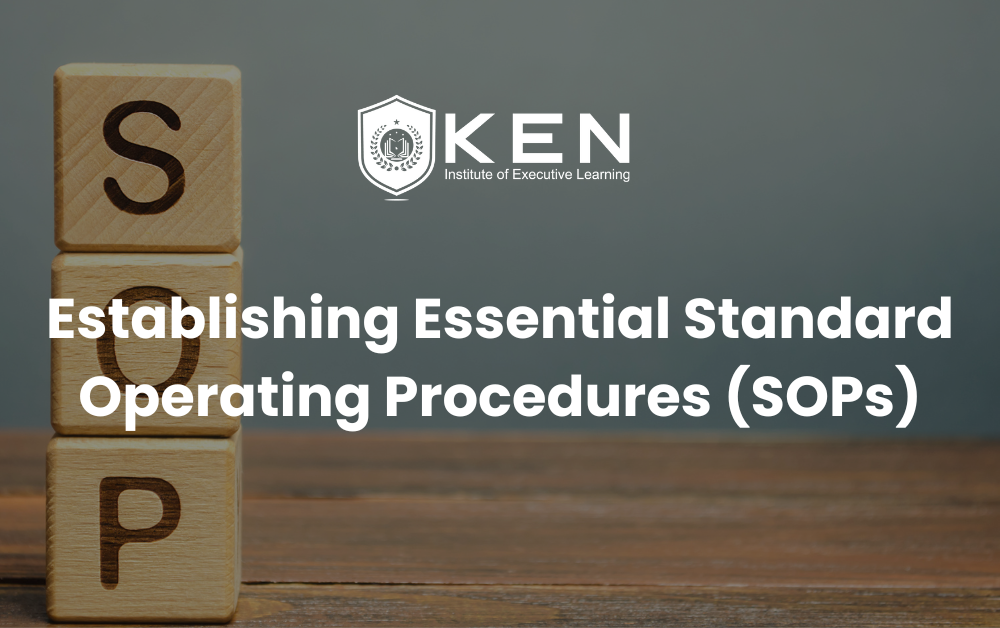
A Standard Operating Procedure (SOP)” is a set of written instructions that document a routine or repetitive activity followed by an organization. Establishing essential SOPs for fire prevention and safety in the workplace is crucial for safeguarding lives, protecting property, and ensuring compliance with fire safety regulations. The development and use of SOPs are an integral part of a successful quality system as it provides individuals with the information to perform a job properly, and facilitates consistency in the quality and integrity of a product or end-result.
Purpose for Establishing Essential Standard Operating Procedures
SOPs describe both technical and fundamental programmatic operational elements of an organization that would be managed under a work plan, Quality Assurance, Project Plan and Quality Manual for Environmental Programs. – They detail the regularly recurring work processes that are to be conducted or followed within an organization. -They document the way activities are to be performed to facilitate consistent conformance to technical and quality system requirements and to support data quality. -They may describe, for example, fundamental programmatic actions and technical actions such as analytical processes, and processes for maintaining, calibrating, and using equipment. -SOPs are intended to be specific to the organization or facility whose activities are described and assist that organization to maintain their quality control and quality assurance processes and ensure compliance with governmental regulations.
Outline of Essential Standard Operating Procedures:
“If not written correctly, SOPs are of limited value. In addition, the best written SOPs will fail if they are not followed. Therefore, the use of SOPs needs to be reviewed and re-enforced by management, preferably the direct supervisor. Current copies of the SOPs also need to be readily accessible for reference in the work areas of those individuals actually performing the activity, either in hard copy or electronic format, otherwise SOPs serve little purpose.”
Fire Risk Assessment
Objective: Identify potential fire hazards and implement preventive measures.
- Inspection schedule: Conduct quarterly or semi-annual fire risk assessments.
- Key areas to assess:
- Electrical systems for faulty wiring or overloaded circuits.
- Storage areas for improper handling of flammable materials.
- Kitchens, workshops, or any area with heat-producing equipment.
- Assessment methods:
- Walkthrough inspections.
- Interviews with employees for observed hazards.
- Review of past fire incidents and near misses.
Fire Prevention Measures
Objective: Minimize the likelihood of fire occurrence.
- Ignition source control:
- Install surge protectors and circuit breakers.
- Use spark arrestors in areas where sparks are likely.
- Flammable material handling:
- Limit quantities of flammable liquids stored on-site.
- Use flameproof cabinets with clear labels.
- Dispose of flammable waste in specialized containers.
- Safe equipment use:
- Establish guidelines for operating high-heat machinery.
- Regularly inspect HVAC systems to prevent overheating.
Fire Detection and Alarm Systems
Objective: Ensure prompt detection and alert of a fire event.
- System components:
- Smoke detectors and heat sensors in critical locations.
- Manual alarm pull stations near exits and high-risk areas.
- Maintenance protocols:
- Test alarms monthly and replace batteries annually.
- Schedule professional system inspections bi-annually.
- Integration:
- Integrate fire alarms with building management systems for automated alerts.
- Consider advanced systems like AI-based smoke detection for large facilities.
Emergency Exit and Evacuation Plans
Objective: Ensure a safe and efficient evacuation during a fire emergency.
- Exit planning:
- Create at least two evacuation routes for each section of the workplace.
- Include alternative routes for blocked pathways.
- Signage:
- Use phot luminescent (glow-in-the-dark) signs for low-visibility conditions.
- Clearly mark exit paths with directional arrows.
- Drill execution:
- Conduct fire drills every 6 months, simulating real-world scenarios.
- Record drill performance and address bottlenecks in the evacuation process.
Firefighting Equipment
Objective: Provide tools for initial fire response and ensure readiness.
- Fire extinguisher types and placement:
- Class A: For ordinary combustibles (paper, wood) near offices.
- Class B: For flammable liquids near storage and labs.
- Class C: For electrical fires near server rooms.
- Training program:
- Conduct hands-on sessions for using extinguishers, fire blankets, and hoses.
- Educate staff on fire classifications and corresponding response strategies.
- Inspection checklist:
- Monthly inspection of fire extinguishers for charge levels and damages.
- Replace any expired or damaged equipment immediately.
Employee Training and Awareness
Objective: Equip employees with knowledge and skills for fire prevention and response.
- Training topics:
- How to identify and report fire hazards.
- Proper use of fire safety equipment.
- Steps to take upon discovering a fire, including the PASS technique (Pull, Aim, Squeeze, Sweep) for extinguishers.
- Frequency: Conduct initial training during onboarding and refresher courses annually.
- Awareness campaigns:
- Use posters, videos, and e-learning modules to reinforce key messages.
- Celebrate fire safety awareness week with engaging activities.
Monitoring and Maintenance
Objective: Sustain fire safety measures through regular oversight.
- Routine inspections: Assign a fire safety officer to oversee daily, weekly, and monthly checks.
- Compliance audits:
- Verify adherence to fire safety standards such as NFPA, OSHA, or local regulations.
- Collaborate with external auditors for unbiased reviews.
- Maintenance logs:
- Keep detailed records of equipment servicing, inspection dates, and maintenance activities.
Reporting and Record-Keeping
Objective: Maintain transparency and facilitate continuous improvement.
- Incident reporting:
- Encourage employees to report hazards anonymously if needed.
- Create a simple form for documenting fire-related incidents or observations.
- Records management:
- Archive reports on training sessions, drills, and risk assessments for at least 5 years.
- Use digital tools for centralized data storage and retrieval.
Collaboration with Authorities
Objective: Leverage expertise and resources from local fire departments and agencies.
- Pre-incident planning:
- Share floor plans and high-risk area maps with the fire department.
- Conduct joint drills for improved coordination.
- Consultations:
- Seek advice on new fire suppression technologies and methods.
- Use professional recommendations to enhance SOPs.
Business Continuity Planning
Objective: Minimize operational disruption and ensure recovery post-incident.
- Critical action items:
- Establish data backup systems stored offsite or in the cloud.
- Pre-identify temporary workspaces to relocate operations.
- Train a crisis management team to handle post-fire recovery.
- Insurance coordination:
- Ensure the facility is adequately insured for fire damages.
- Keep updated records of assets and inventory for claim processing.
Summary
The development and use of SOPs minimizes variation and promotes quality through consistent implementation of a process or procedure within the organization, even if there are temporary or permanent personnel changes. SOPs can indicate compliance with organizational EPA QA/G-6 1 April 2007 and governmental requirements and can be used as a part of a personnel training program, since they should provide detailed work instructions.
It minimizes opportunities for miscommunication and can address safety concerns. When historical data are being evaluated for current use, SOPs can also be valuable for reconstructing project activities when no other references are available. In addition, SOPs are frequently used as checklists by inspectors when auditing procedures.
Ultimately, the benefits of a valid SOP are reduced work effort, along with improved comparability, credibility, and legal defensibility. By implementing these comprehensive SOPs, workplaces can proactively address fire risks, ensure compliance with regulations, and create a safe environment for employees and stakeholders.
Join online courses in OHSE, Fire Safety, Environment and Sustainability and Mechanical Engineering for professionals to advance their studies alongside their work commitments. Take advantage of the expert faculty’s and the flexibility of 100% online learning.
Join Ken Institute and unlock a world of online courses in Occupational Health and Safety, Fire Safety, and Environment and Sustainability and Mechanical Engineering. Propel your career to new heights.
Get in touch with us at: info@keninstitute.com
Visit our website: www.keninstitute.com
Call us on +917569034271
Let’s connect together on: Facebook, YouTube, LinkedIn, and Instagram.