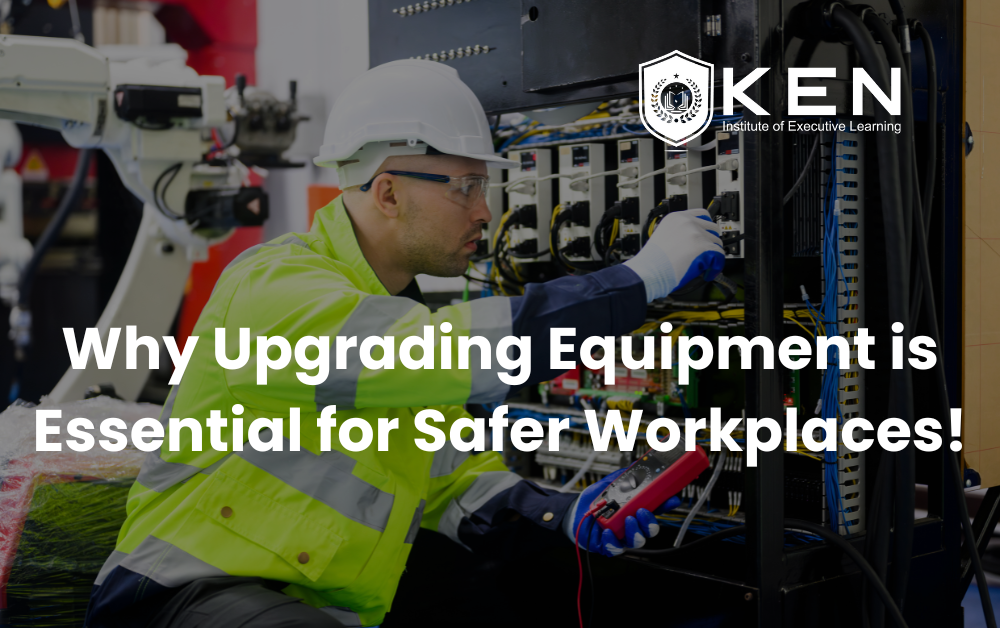
Workplace safety is a top priority for any organization, particularly in industries with high-risk environments such as construction, manufacturing, healthcare, and logistics. One of the most effective ways to enhance safety is by regularly upgrading equipment. Upgrading equipment is not just an operational improvement, it’s a critical investment in workplace safety. By ensuring compliance, enhancing reliability, and reducing risks, businesses can create a safer environment, boosting both worker morale and productivity while avoiding costly incidents.
The key reasons why upgrading equipment is essential for safer workplaces:
1. Improved Safety Standards and Compliance
Regulatory bodies, such as OSHA (Occupational Safety and Health Administration), frequently update safety standards. Older equipment may not meet current requirements, putting workers at risk and exposing businesses to legal penalties. Upgrading ensures compliance with the latest regulations, minimizing potential liabilities.
2. Enhanced Reliability and Performance
Outdated equipment tends to break down more frequently, increasing the likelihood of workplace accidents. Newer models are designed to be more reliable, incorporating features such as better guards, automated shutdowns, and improved stability. This reduces the risk of malfunction-related injuries.
3. Introduction of Advanced Safety Features
Modern equipment often comes with advanced safety features, such as:
- Automatic sensors that detect unsafe conditions.
- Ergonomic designs that reduce physical strain on workers.
- AI-driven monitoring systems that predict potential hazards.
These improvements significantly reduce the likelihood of incidents.
4. Reduced Downtime and Stress on Workers
Frequent equipment failures lead to unplanned downtime and rushed repairs. This can result in stress for workers, increasing the likelihood of human errors. Upgrading to more reliable equipment ensures smooth operations, giving workers a safer and less stressful environment.
5. Increased Worker Confidence and Morale
When workers see that management is investing in safer, modern equipment, it demonstrates a commitment to their well-being. This boosts morale, productivity, and encourages employees to follow safety protocols more closely.
6. Cost Savings in the Long Run
While upgrading equipment can be costly upfront, it leads to long-term savings by:
- Reducing medical expenses from workplace injuries.
- Lowering insurance premiums due to a better safety record.
- Avoiding fines and penalties related to safety violations.
Additionally, newer equipment often operates more efficiently, reducing energy costs.
Industry Examples: How Upgrading Equipment Improves Workplace Safety
1. Construction Industry
Old Equipment Risks:
- Older machinery such as cranes, excavators, and bulldozers may lack modern safety controls, increasing the risk of tipping or operator error.
- Traditional personal protective equipment (PPE), like basic hard hats or gloves, may not offer optimal protection.
Upgraded Equipment Benefits:
- Smart cranes with load sensors and automated stability control prevent tipping incidents.
- Enhanced PPE, such as smart helmets with built-in sensors and cameras, alerts workers of nearby dangers.
- Exoskeleton suits reduce the risk of back injuries by supporting heavy lifting.
Result: Upgraded equipment in construction reduces injuries related to heavy machinery operation and improves overall site safety.
2. Manufacturing Industry
Old Equipment Risks:
- Manual handling of heavy materials or repetitive tasks often leads to musculoskeletal disorders.
- Outdated conveyor belts and machines lacking proper guards can result in serious injuries like amputations.
Upgraded Equipment Benefits:
- Automated robotic arms handle repetitive or dangerous tasks, reducing the risk of human error.
- Conveyor systems with emergency stop functions and built-in machine guards protect workers from accidental contact.
- Advanced ventilation systems reduce exposure to harmful fumes or particulates.
Result: Modernized equipment in manufacturing reduces injuries from repetitive stress and machine-related accidents while improving air quality for workers.
3. Healthcare Industry
Old Equipment Risks:
- Traditional patient handling methods increase the risk of back and joint injuries for healthcare workers.
- Older sterilization equipment may not be as effective, increasing the risk of infections.
Upgraded Equipment Benefits:
- Powered patient lifts and transfer devices reduce strain on healthcare workers, minimizing lifting-related injuries.
- Modern sterilization units ensure higher levels of hygiene, protecting both staff and patients.
- Wearable monitoring devices allow real-time tracking of workers’ health conditions, preventing fatigue-related accidents.
Result: Upgrading healthcare equipment leads to fewer staff injuries, lower infection rates, and improved patient outcomes.
4. Warehousing and Logistics Industry
Old Equipment Risks:
- Manual forklifts without modern features can cause accidents, such as tipping or collision.
- Older shelving systems may collapse under excessive loads if improperly maintained.
Upgraded Equipment Benefits:
- Autonomous forklifts equipped with collision detection systems and cameras reduce operator error.
- Smart shelving systems with load sensors alert workers before overloading occurs.
- Wearable safety vests with GPS tracking improve worker visibility and reduce collision risks in busy warehouses.
Result: Equipment upgrades in warehouses improve material handling safety and reduce accident rates significantly.
5. Oil and Gas Industry
Old Equipment Risks:
- Aging drilling rigs and equipment often suffer from corrosion, increasing the risk of blowouts.
- Outdated personal gas detectors may not detect all hazardous gases in time.
Upgraded Equipment Benefits:
- Smart drilling rigs with advanced sensors monitor pressure changes and potential equipment failure in real time.
- Multi-gas detectors with wireless connectivity instantly alert control rooms about dangerous gas levels.
- Wearable fatigue monitoring devices detect early signs of worker exhaustion, preventing accidents caused by fatigue.
Result: Upgraded technology in oil and gas operations reduces catastrophic failures and enhances worker safety in high-risk environments.
6. Food Processing Industry
Old Equipment Risks:
- Older processing machinery may have exposed moving parts, leading to cuts or crush injuries.
- Inconsistent refrigeration systems can lead to food contamination.
Upgraded Equipment Benefits:
- Modern food processing machines include improved safety interlocks and automatic shut-off mechanisms.
- Advanced refrigeration units maintain stable temperatures with real-time monitoring, ensuring product safety.
- Sanitation systems with automated cleaning cycles reduce manual handling of hazardous cleaning agents.
Result: Upgraded equipment in food processing ensures both worker safety and food quality, preventing accidents and product recalls.
Areas for Improvement for Equipment Upgrades
Based on a preliminary assessment, the following areas have been identified as priorities for equipment upgrades in various industries:
Construction
- Cranes and forklifts with load sensors and stability controls.
- Personal protective equipment (PPE) with smart technology for hazard detection.
Manufacturing
- Automated assembly lines with emergency stop features and machine guards.
- Ventilation systems with real-time air quality monitoring.
Healthcare
- Patient handling equipment such as motorized lifts to prevent strain injuries.
- Sterilization units with advanced hygiene controls.
Logistics
- Autonomous forklifts equipped with collision detection systems.
- Smart shelving systems with load capacity monitoring.
Phased Implementation Plan for Upgrading Equipment
Phase 1: Assessment and Planning (1-2 Months)
- Conduct a detailed assessment of all existing equipment.
- Identify critical areas where immediate upgrades are necessary.
- Consult with equipment vendors to obtain quotes and specifications.
Phase 2: Procurement and Testing (3-4 Months)
- Procure new equipment in batches, prioritizing high-risk areas.
- Conduct thorough testing and quality assurance on the newly acquired equipment.
- Train employees on proper usage and safety protocols.
Phase 3: Deployment (2-3 Months)
- Gradually deploy the upgraded equipment across different departments.
- Provide on-site support to ensure a smooth transition.
- Monitor safety improvements and gather feedback from employees.
Phase 4: Evaluation and Continuous Improvement (Ongoing)
- Conduct regular evaluations to assess the effectiveness of the upgrades.
- Make further improvements based on employee feedback and evolving safety standards.
- Schedule periodic maintenance to keep equipment in optimal condition.
Summary
Each industry faces unique risks, upgrading equipment is a proactive measure that will significantly enhance workplace safety, improve compliance, and boost overall productivity. Â By investing in modern technology, the organization can create a safer, more efficient working environment, benefiting both employees and the bottom line.
Join us to create a world where every worker returns home safely at the end of each day! We aim to educate, inform, and inspire both employees and employers about the best practices in occupational health and safety.
Join Ken Institute and unlock a world of online courses in Occupational Health and Safety, Fire Safety, and Environment and Sustainability and Mechanical Engineering. Propel your career to new heights.
Get in touch with us at:Â Â info@keninstitute.com
Visit our website:Â Â www.keninstitute.com
Call us on +917569034271
Let’s connect together on: Facebook, YouTube, LinkedIn, and Instagram.