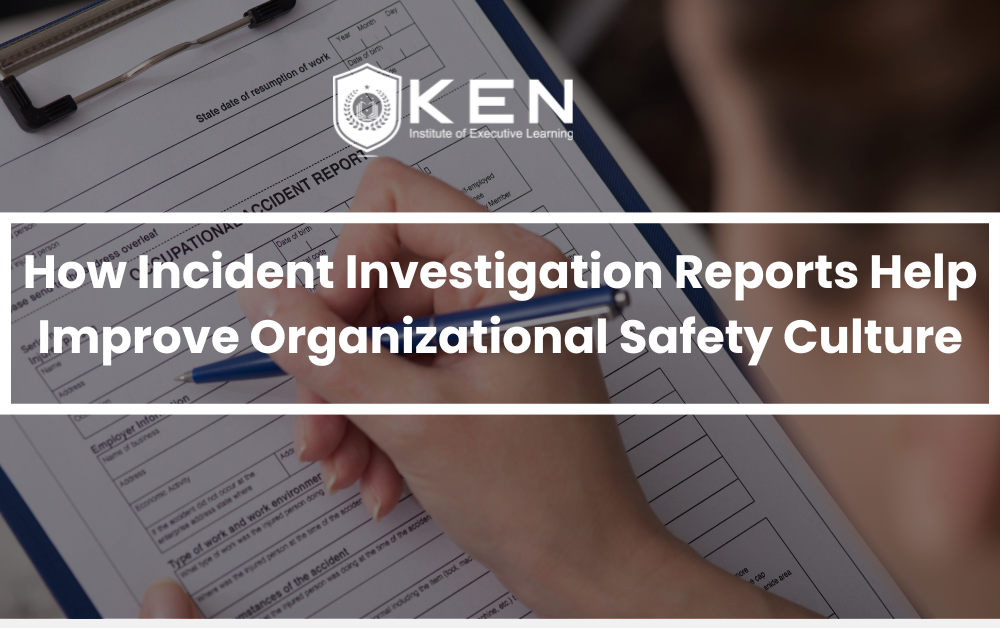
Incident investigation reports are the documents that play a crucial role in strengthening an organization’s safety culture. The report is record of details of events, including accidents, near misses, or process failures, to understand their causes and prevent recurrence. These reports help organizations identify risks, improve safety, and ensure compliance.
Incident investigation reports aren’t just about checking a box, they’re about learning, evolving, and reinforcing safety as a core value.
Purpose and Importance of Incident investigation reports:
Documentation:
Incident reports serve as a record of events, capturing details like who was involved, what happened, when and where it occurred, and the contributing factors.
Investigation:
They facilitate the investigation process, allowing organizations to analyze incidents, identify root causes, and implement corrective actions.
Risk Management:
By analyzing incident reports, organizations can identify trends, patterns, and potential hazards, leading to proactive risk management and safety improvements.
Compliance:
Many industries and regulations require organizations to investigate and report incidents, ensuring accountability and promoting a safe work environment.
Key Elements of an Incident Investigation Report:
Identifying Root Causes
- Investigation reports dig beyond the surface to uncover the real reasons incidents happen—not just who did what, but why it happened.
Image Source: slideplayer.com
- They often reveal systemic issues, like poor communication, lack of training, or inadequate procedures, rather than just individual mistakes.
Driving Corrective Actions
- Once causes are known, reports recommend corrective and preventive actions (CAPAs) to eliminate risks.
- Implementing these actions reduces the chance of similar incidents happening again.
Promoting Learning and Awareness
- Well-documented reports become learning tools.
- Sharing findings across teams helps spread awareness, reminding everyone what can go wrong and how to prevent it.
Increasing Transparency and Trust
- When employees see that incidents are taken seriously and that outcomes are shared, it builds trust in leadership.
- A transparent approach encourages more people to report near-misses and hazards, knowing their input leads to positive change.
Measuring Safety Culture Maturity
- Over time, analyzing trends in investigation reports helps gauge how mature the safety culture is.
- A decrease in repeat incidents or more proactive reporting signals cultural improvement.
Image Source: researchgate.net
Employee Involvement
- Engaging employees in the investigation process makes them feel valued and reinforces shared responsibility for safety.
- It fosters a “no blame” culture, focusing on improvement instead of punishment.
Types of Incident Reports:
- Workplace Injury Reports:Document injuries sustained by employees or others in the workplace.
- Accident Reports:Detail accidents that occur in the workplace, including near misses and property damage.
- Near-Miss Reports:Document incidents that did not result in injury or damage, but could have.
- Equipment Failure Reports:Record incidents involving equipment malfunctions or failures.
- Security Incident Reports:Document security breaches or threats.
- HR Incident Reports:Document events or issues involving employees in the workplace
Turning Incident Investigations Into Safety Learning Tools

Image Source: Resco.net
Incident investigation reports when used well, they are one of the most powerful tools to build a resilient, proactive, and trustworthy safety culture.
Step 1: Collect Facts, Not Blame
- Interview witnesses
- Gather photos, logs, equipment data
- Record the sequence of events objectively
Step 2: Analyze the Root Cause
- Use tools like the “5 Whys” or Fishbone Diagram
Image Source: Mobile2b
- Identify contributing factors (e.g., procedures, training, equipment, communication)
Step 3: Document the Findings Clearly
- Keep it factual, simple, and structured
- Avoid jargon or emotional language
Step 4: Recommend Preventive Actions
- Solutions should be practical and measurable
- Assign owners and deadlines for each action
Step 5: Share and Learn
- Use reports in toolbox talks, safety meetings, and on boarding
- Encourage open discussion and feedback
Sample Incident Investigation Report (Template)
Incident Title: Slip and Fall in Loading Bay
Date of Incident: March 29, 2025
Location: Warehouse Loading Bay A
Reported by: James Carter, Warehouse Supervisor
Date Report Completed: April 1, 2025
Incident Description
At 9:10 AM, an employee slipped on a wet surface while unloading a pallet. The employee fell backward and sustained a minor back injury. No equipment damage occurred.
Immediate Actions Taken
- First aid provided on-site
- Area cordoned off
- Spill cleaned up
- Safety officer notified
Investigation Team
- Safety Manager
- Warehouse Supervisor
- Employee Representative
Root Cause Analysis (5 Whys Example)
Why did the employee slip?
– The floor was wet.
Why was the floor wet?
– A water spill was not cleaned up promptly.
Why wasn’t it cleaned up?
– The spill was not noticed in time.
Why wasn’t it noticed?
– There is no designated person to monitor the loading bay for hazards.
Why is there no designated person?
– Current safety protocols don’t assign responsibility for area checks.
Contributing Factors
- Lack of clear cleaning responsibility
- No visible “wet floor” signs available
- Inadequate hazard communication between shifts
Corrective Actions
Action | Owner | Deadline |
Assign loading bay inspection duties to shift leads | Safety Manager | April 5, 2025 |
Place wet floor signs in all hazard-prone areas | Maintenance Lead | April 6, 2025 |
Conduct refresher training on hazard identification | HR & Safety | April 12, 2025 |
Lessons Learned
- Clear responsibilities and better communication between shifts can prevent similar incidents.
- Employees need quick access to basic safety tools like signs and cleaning materials.
Report Distribution
- Warehouse team
- Safety department
- Site manager
Summary
OSHA suggests referring to unplanned adverse events as incidents rather than accidents. OSHA holds that nearly all of these events could be prevented with greater awareness of the hazards, better control measures, and stronger safety programs.
Image Source: Vector Solutions
The procedures of incident investigations encourages employers and safety professionals to identify root causes rather than chalking it up as a random occurrence or a freak accident. It also holds them accountable for mitigating risks and taking steps to prevent future incidents.
Amplify Your HSE Journey with KEN Institute!
Join a global network across 63 countries and advance your career with flexible online courses in Occupational Health and Safety, Fire Safety, Environment and Sustainability and Mechanical Engineering.
Subscribe our blogs for regular updates, share your experiences, and engage in discussions.
Connect now and take the next step toward professional excellence!
Get in touch with us at: info@keninstitute.com
Visit our website: www.keninstitute.com
Call us on +917569034271
Let’s connect together on: Facebook, YouTube, LinkedIn, and Instagram.